Base oil Selection Beyond the Bench
Compoundings Magazine
February, 2001
By Thomas F. Glenn, Petroleum Trends International, Inc
Although mergers, acquisitions,
and exists have reduced the number of US base oil suppliers, the
number of options lubricant manufactures have to consider when formulating
finished lubricants has risen sharply. This is due primarily to
the emergence of Group II, II+ and III base oils over the last five
years. Blending is a much more complicated activity today than it
has been in the past and there is considerable room for success
and failure in the choices that are made.
At one level, success and failure
will be measured by the impact base oil selection has directly on
the costs of good sold. A decision to use a typical Group I instead
of Group II to blend a 10W-30 passenger car motor oil (PCMO), for
example, can cost a manufacturer as much as $0.10 a gallon more
in total formulation costs for that product. This could be a very
costly mistake if 10W-30 PCMO is the primary product in the suppliers
portfolio. The opposite could be true, however, if a blender uses
Group II to manufacture its industrial lubricants and only has a
small share of its business in PCMO. Although these examples may
present what appear to be obvious and relatively easy blending challenges
to resolve, they can get very complicated when one factors in other
considerations. These include differences in product portfolios,
supply line assurances, contract issues, tankage limitations, competitive
positioning, supply and blending logistics, and variation in base
oil quality, among others. As shown in Figure 1, base oil
costs can vary considerably if a blender does not optimized inventory
around product portfolios.
Base oil quality does vary even
within a given API Group and viscosity grade, and this variability
caninfluence total formulation costs. The aromatic content of a
heavy Group II, for example, can vary as much as 4 to 5% between
suppliers. Differences of several VI units between suppliers of
light and medium neutrals are also not unusual. For some, these
variations in VI open the doors for opportunistic ways to reduce
costs by backing out VI improver. For others, however, they could
result in cost burdens, or tradeoffs in volatility or low temperature
performance. Even greater differences in quality and impacts on
costs can be seen in the supply of Group I. In fact, some Group
I base oils are very near in quality to Group II, whereas others
have a long way to go.
Lubricant manufactures are now
challenged to optimize base oil costs and performance across product
lines with increasingly different appetites and thresholds of sensitivity
on price and performance. In some cases this process may require
a decision to install more base oil storage tanks. In others, it
may require forming a strategic alliance with another lubricant
manufacture in an effort to optimize costs through reciprocal manufacturing
agreements that allow each member of the alliance to focus on its
most profitable business segments. Still others may find the best
solution is to outsource manufacturing of a given product line,
or simply drop it all together.
These and other decisions go well
beyond simply the cost of goods sold for a given product in the
portfolio. Base oil selection will increasingly have strategic implications
that can result in long-term competitive advantages and disadvantages.
As a result, although formulation of lubricants at the bench top
is clearly best left in the hands of chemists and other professionals
with similar expertise,the probability of economic success beyond
the bench can be greatly increased if base oil selection is assessed
within the context of the companys overall business strategy
and includes ongoing dialog with business managers, sales and marketing
and others in the organization.
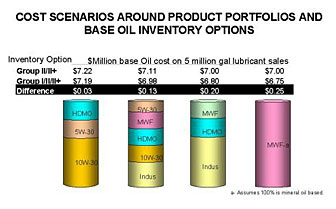
Copyright © Petroleum Trends International,
Inc. 2002
|