National Petrochemical
& Refiners Association
1899 L Street, NW, Suite 1000
Washington, DC 20036
LW-01-137
A US MARKET SPACE ANALYSIS
OF GTL LUBRICANTS
By
Thomas F. Glenn
President
Petroleum Trends International, Inc.
Metuchen, NJ
Presented at the
NPRA
Lubricants & Waxes Meeting
November 8-9, 2001
Omni Houston Hotel
Houston, TX

Publication of this paper does not signify
that the contents necessarily reflect the opinions of the NPRA,
its officers, directors, members, or staff. NPRA claims no copyright
in this work. Requests for authorization to quote or use
the contents should be addressed directly to the author(s)
ABSTRACT
Gas-to-liquid (GTL) processing
provides a means to convert natural gas to such products as diesel
fuel, jet fuel, naphtha, base oil, wax, olefins, and alcohols. The
products produced by GTL are typically exceedingly clean. In addition,
they have very favorable manufacturing economics.
Lubricant base oils produced
by GTL processing are expected in the market in the 2005/2006 timeframe.
They are expected to initially enter the market by competing with
Group III and IV in the synthetic and synthetic-blend engine oil
market space. To a lesser extent, GTL base oils will also compete
with Group II+ as a correction fluid for Group I in 10W-30 formulations,
and as a workhorse against Group II+ in a growing market for 5W-30.
Rather than reducing the value of GTL by moving down the quality
continuum to Group I and II base oils, GTL base oils are expected
to reside in the high-end market space of Group II+, III, and IV
and be the beneficiaries of demand being pushed into this market
space by more stringent specifications.
In addition to GTL competing
in the emerging low viscosity passenger car motor oils markets,
it will also penetrate automotive driveline applications, premium
diesel engine oils, and high-end industrial lubricant applications
over the next five to eight years.
ACKNOWLEDGEMENTS
This paper is based on primary research conducted
by PetroTrends professional staff over the last three months. In
addition, it includes information derived from such secondary resources
as the Internet, and other public domain documentation. It is also
supplemented by information and insights provided by Nexant Chem
Systems. Nexant Chem Systems is a market research and consulting
firm. The firm recently completed a multiclient study focusing on
the manufacturing economics of GTL; Stranded Gas Utilization: Methane
Refineries of the Future."
PetroTrends would also like to acknowledge Syntroleum
for sharing its insights on some of the typical performance characteristics
for GTL base oils.
BACKGROUND
The technology of converting gas to liquids
(GTL), is based on the chemical process known as Fischer-Tropsch
(FT) synthesis. The products produced by GTL include naphtha,
kerosene, jet and diesel fuels. In addition, GTL plants also produce
such specialty products as lubricant base oils, waxes, olefins,
and alcohols.
Interest in GTL has grown rapidly over the last
five years for several reasons. First, it provides a means to monetize
significantly more of the worlds natural gas reserves. These
reserves are estimated at over 14,000 TCF and hold the potential
to produce an equivalent of several hundred billion barrels of crude
oil. According to a study on GTL by Arthur D. Little, an estimated
900 TCF of gas reserves are potentially suitable for monetization
by GTL technology. A significant percentage of these reserves
are located in regions where there is little to no domestic demand
or too far from export markets to have much economic value.
Beyond the value of generating more equivalent
crude, however, GTL provides an economically attractive means to
produce fuels and specialty products far cleaner then those derived
from traditional crude oil processing. This is particularly important
in light of the increasingly stringent diesel fuel regulations coming
into play. In the US, for example, the United States Environmental
Protection Agency (EPA) will mandate a maximum of 15 parts per million
(ppm) sulfur level in diesel fuel in 2006. Even more restrictive
regulations are expected in Europe. In May of this year, the European
Commission proposed phasing in a 10 ppm limit on sulfur starting
in 2005. Similar requirements are also on the horizon in Japan and
other countries. These and other sulfur limits on the horizon will
be a significant challenge for refiners to meet when one considers
that the average level of sulfur in much of the diesel produced
today is roughly 300 to 350 ppm.
Diesel fuel produced by the GTL process is exceedingly
clean. It has no detectable levels of sulfur or aromatics. It also
has significantly higher cetane numbers than its crude oil derived
counterpart. Diesel produced by the GTL process can be used directly
as ultra high quality fuel, or as a blend component to boost the
performance of lower quality traditional diesel fuel. Similarly,
GTL processing also produces high quality (e.g. low sulfur, low
aromatic content) kerosene, jet fuel, naphtha and a number of such
specialty products as olefins, waxes, lubricant base oils, and others.
In addition to producing very high quality,
environmentally desirable synthetic fuels, or synfuels
and specialty products, GTL is also attracting a high degree of
interest because it provides a means to eliminate flaring and/or
reinjecting natural gas. Flaring is considered an environmental
issue and technology that eliminates it has value. Although somewhat
a longer-term issue, GTL also holds promise as a fuel source for
fuel cells. Fuel cells are expected to begin penetrating the internal
combustion (IC) engine market in roughly five years. The reformers
used in automotive fuel cell applications will have an appetite
for only the cleanest fuels, and GTL fuel can offer the desired
level of purity.
Driven by the opportunity to monitize natural
gas, and the other issues mentioned, interest in GTL has climbed
over the last few years. Currently there are 13 announced GTL projects
in the world. Taken together they have the potential to produce
an estimated 870 thousand barrels a day (TBD). The most active regions
in terms of number of plants are Qatar and Australia; three plants
have been announced for each. Egypt is also expected to be a hotbed
of GTL production with two announced plants with a combined capacity
estimated at 145 TBD, as shown in Table 1.
Table 1
ANNOUNCED GAS-TO-LIQUID PLANTS AS OF OCTOBER 2001
|
Location
|
|
Qatar
|
290
|
Egypt
|
145
|
Austrailia
|
115
|
Argentina
|
75
|
Trinidad
|
75
|
Indonesia
|
70
|
Iran
|
70
|
Nigeria
|
30
|
Total
|
870
|
Although much of the current interest in GTL
is tied to monitizing stranded gas to produce high quality diesel
fuel, it has also garnered interest due to its ability to generate
high quality specialty products, including lubricant base oil, waxes,
and olefins. In fact, there are two companies currently using Fischer-Tropsch
reactions to produce synthetic waxes. Schümann
Sasol operates a plant in South Africa and Shell operates a plant
in Bintulu Malaysia. The Shell plant uses the Fischer-Tropsch reaction
in the Shell Middle Distillate Synthesis (SMDS) process to convert
long-chain paraffinic feed into wax and other specialty products.
Both the products produced by Shell and Schümann Sasol have
very high purity and sharp hydrocarbon distributions. These products
are typically hard waxes with very high melting points (e.g. above
200°F)
Unlike petroleum wax, which is a mix of iso-
and normal paraffins, F-T wax is pure normal paraffin in the C20
to C60+ range. The characteristics of F-T waxes give them a significant
advantage over traditional petroleum waxes in such high-melt applications
as hot-melt adhesives, powdered coatings, inks, textiles, color
concentrates, and plastics. In addition, F-T waxes are also advancing
into the phase change materials (PCM) market. This includes such
applications as heating systems, food transportation, medical devices
and therapies, and other applications where the latent heat available
from phase change can be put to work. The global market in the high
melt space is roughly 80 to 90 million pounds, valued at roughly
$50 million, or about 1% of the total global wax demand. Although
F-T waxes offer clear advantages in some applications, in others
they are disadvantaged due to normal paraffin content and narrow
hydrocarbon distribution. This hydrocarbon profile does not currently
afford the same formulation and cut point flexibility found in petroleum
waxes and in a market as diverse and diffuse as the wax business,
formulation flexibility offers a distinct advantage to wax suppliers.
Opportunities in the wax market and how GTL
waxes might compete in this market space do weigh into the economics
of building plants. As a result, the outlook for GTL base oil is
also a function of the outlook for wax from these plants. This is
not to say that one could not justify the economics of a GTL base
oil plant without wax, but it does suggest that the economics of
a specialty GTL plant could be improved if high-value wax were part
of the product mix. As it does relate to the outlook for GTL base
oil production, additional background on GTL wax and how its market
space is likely to develop follows.
GTL wax. Most of the wax in the market today
is derived from base oil production. Although certainly a valued
product, technically it is a byproduct of classic solvent refining
solvent dewaxing base oil production. Unfortunately, as a
byproduct of base oil production, the future of the petroleum wax
business is not in its own hands. Instead, it is in the hands of
the lube base oil unit, and times are changing.
Lubricant base oil manufacturers are feeling
pressure to incorporate catalytic dewaxing technology to meet increasingly
stringent base oil performance requirements. The catalytic dewaxing
process does not yield wax. Instead, the wax molecules are cracked
and isomerized into base oil, fuels, and other fractions. The impact
of this shift has been felt greatest in the North American market.
In the last five years, a major grassroots base oil plant was built
(Excel Paralubes) using catalytic dewaxing and three others replaced
existing solvent dewaxing technology with catalytic dewaxing. Others
are expected to follow. In addition, Petro-Canada added ISODEWAXING
capacity to its plant in late 1996. In addition to declines in wax
supply as a result of conversions from solvent dewaxing to catalytic
dewaxing, supply in North America has been further eroded by the
exits of several smaller base oil producers. These exits took wax
with them.
As discussed, how the market space for GTL base
oils develops will, in part, be influenced by the business opportunities
associated with the wax market and how these opportunities might
compete with other interests. GTL projects are considered to have
the potential to greatly increase wax supply because roughly 50%
of the yield from the syngas reactor is wax. The economics of world
scale GTL plants, however, will be driven by demand for low sulfur
diesel fuel, not wax and other specialty products.
Beyond the big picture economic realities of
a world scale GTL plant, a number of the major oil companies (those
with the resources to build a world scale GTL plant) would also
have to look across their businesses before heading into the wax
market. Many of the majors still produce wax from solvent dewaxing.
These companies will likely face the prospects of cannibalizing
their existing wax business should they decide to market wax from
a GTL plant. For some, this may prove to be a losing proposition
where every pound of wax moved into the market from the GTL plant
displaces a pound of wax they have already placed in the market
and produced from its solvent dewaxing unit.
The next likely new entrant into the F-T wax
supply pool would be a specialty products supplier with its eyes
on base oils, wax and other specialty GTL products. This would likely
be a producer with no ties to a conventional solvent-refining/ solvent-dewaxing
lube base oil plant. Such a player would not have to consider the
issue of cannibalization and could develop the high-melt wax market
competing aggressively in an effort to grab market share. Although
a specialty products GTL player could potentially do this, the value
of this effort is questionable since the high-melt point wax market
is fairly well balanced. It is also important to note that a new
entrant into the F-T wax market in the high-melt market space would
be competing with entrenched suppliers. They would also be competing
with PE wax suppliers. PE wax is already a formidable competitor
with F-T in the high-melt market space.
A new F-T wax producer could also decide to
target the large market spaces occupied by mid- and low- melts petroleum
waxes. This, however, is not a straightforward process. F-T wax
suppliers would likely find it necessary to fractionate the wax
because the C20 to C60 range of normal paraffins is too wide for
most applications. They may also find it necessary in many applications
to blend F-T wax with petroleum waxes in order to match performance
requirements with existing expectations. Even with the cost burden
of fractionation and blending, the cost structure for F-T wax could
prove an advantage. In assessing the magnitude of this advantage,
however, one would have to remain grounded in the fact that a decision
to compete in this market space is a decision to compete with a
large volume of byproduct coming from lubricant base oil production.
In summary, this means that the primary driver
for GTL plants today is high-quality, environmentally friendly diesel
fuel, not lubricant base oils, waxes, and other specialty products.
The catalysts used in a plant designed to produce GTL fuel and the
alpha value of its products do not readily lend themselves to base
oil production.
BASE OIL MARKET SPACE DEVELOPMENT
Few question if the market for GTL base oils
will develop. The primary questions asked today are when, where
and how will it develop, and who will develop it first. In addition,
there is a good deal of interest in the economics of these plants.
Insight into these and other questions starts with an understanding
of what GTL base oils are and what level of performance they offer.
GTL base oils are products synthesized by a
Fischer-Tropsch reaction. These base oils have no detectable levels
of sulfur, nitrogen, or aromatics, and they are water white. They
have a very narrow hydrocarbon distribution and excellent oxidation
stability characteristics. In addition, the lower viscosity products
(e.g. less than 4cSt) are typically biodegradable. GTL base oils
with viscosity grades used in automotive engine oil applications
(4.0 to 9.0 cSt) are expected to have a Viscosity Index in the range
of 140 to 155. By comparison, PAO has a VI of 120 to 138 for the
same viscosity range.
Another very important attribute of GTL base
oils and one that will shape its place in the market is its volatility.
GTL base oils reportedly have NOACK volatilities significantly lower
than API Group I, II/II+ and III base oils. A 4 cSt product, for
example, is reported to have a NOACK volatility several percentage
points below 10, as compared to a typical Group III with a NOACK
in the low- to mid- teens. These performance attributes position
GTL base oils well to compete with PAO and Group II+ and III in
the automotive lubricants market space. It also suggests that the
greatest value for GTL base oils will be realized in the automotive
lubricant viscosity grade ranges of 2 cSt to roughly 10 cSt and
that alpha values for specialty GTL product producers will likely
optimize on these grades.
GTL base oils also have excellent low temperature
properties. In fact, they appear to be only slightly disadvantaged
when compared to PAOs cold crank viscosities. The pour point
of GTL base oils is, however, much closer to that of a Group II/III
than it is to a PAO. This can be addressed by the use of pour point
depressant and GTL base oils are reported to have excellent responsiveness
to methacrylate -based pour point depressants.
In addition to high quality, GTL base oils also
have very favorable manufacturing economics. According to a multiclient
study recently completed by Nextant Chem Systems, the manufacturing
costs for GTL delivered in the US market are comparable with that
of Group I, II, and II+. Even more importantly, ChemSystems' analysis
reveals that the economics for GTL are more favorable than that
of high VI Group III, as shown in Figure 1.
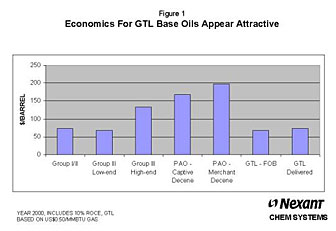
Considering the manufacturing
cost position of GTL base oils and its performance characteristics,
a starting point to begin modeling market space development for
GTL base oils is one that looks at how the market space for API
Group II and III developed. These products also entered the market
as high performance base oils with attractive manufacturing economics.
An analysis of how the market space for Group II and III base
oils developed is provided as a backdrop for how the market space
for GTL base oils might also develop
Group II and
III base oils. Group II and III base oils
are product definitions that have emerged over the last decade.
The American Petroleum Institute (API) developed the API base oil
group categories in an effort to differentiate the various levels
of base oils quality in the marketplace. In addition to placing
polyalphaolefin (PAO) in a class of its own (GROUP IV). The system
established three groups of paraffinic base oils. These groups were
based on saturates, sulfur, and viscosity index (VI), as shown in
Table 2.
Table 2
American Petroleum Institute Paraffinic Basestock Groups
|
|
Requirements
|
API Group
|
Sulfur, % wt.
|
Saturates, % wt.
|
Viscosity index
|
l
|
>0.03 and/or
|
<90
|
80-119
|
ll
|
£0.03 and
|
Ž90
|
80-119
|
lll
|
£0.03 and
|
Ž90
|
Ž120
|
lV - a
|
-
|
-
|
-
|
V - b
|
-
|
-
|
-
|
a - includes polyalphaolefin (PAO).
b - includes esters and other basestocks
not included in API Groups l through lV.
|
Group II and III base oils are generally considered
superior to Group I because they have a lower aromatic content and
higher viscosity index. Aromatic fractions tend to be more unstable
than saturated hydrocarbons, and as a result, Group II base oils
have superior thermal stability and resistance to oxidation over
Group I. In addition, as you move up the continuum from Group II
to III, you move from base oils with a minimum VI of 95 to Group
III base oils with minimum VI over 120. This higher VI, together
with aromaticity and other issues, makes Group III base oils an
ideal blend stock to meet the more stringent volatility requirements
in passenger car motor oil. In addition, it gives these base oils
an advantage in heavy-duty motor oil, and ATF.
Although the API Group classifications do provide
clear guidelines to differentiate conventional and unconventional
base oils, it is important to consider the differences between API
Groups as a quality continuum based primarily on saturates and VI,
as shown in Figure 2.
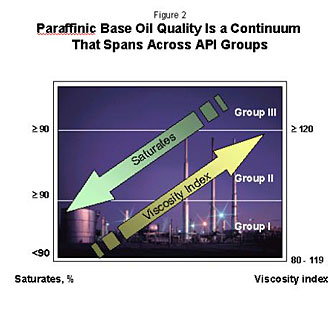
The importance of this continuum gave rise to
the Group II+ designation. Although Group II+ is not
an official API definition; it emerged out of the need to describe
base oils with a meaningfully higher viscosity index than the 100
than is typical of most Group II base oils. Group II+ base oils
typically have VI in the range of 108 to 115. These base oils offer
performance advantages over Group II in some passenger car motor
oil applications, specifically related to balancing volatility with
low temperature viscometrics.
Where GTL base oils will fit in the API base
classification system has yet to be determined. Based on some of
the performance data currently being developed, however, it is believed
that GTL base oils would likely be handled in one of three ways.
One possibility is that another API group will be established to
accommodate it. Another possibility is that it will simply fall
into a Group III designation because it does, in fact, meet the
criteria for a Group III. Another possibility is that GTL base oils
will follow the path of Group II+. This is likely to result in a
market-place designation of Group III+. As shown in Figure 3, the
performance of GTL is considered nearly equal to Group III, however,
it could enjoy significantly lower manufacturing costs. The cost
and performance of GTL base oils suggest it will likely track a
market space development path similar to that of III, and to a lesser
extent, Group II+.
The market space for Group II+ and Group III
was developed on several fronts, including:
- Direct competition with PAO
- Low volatility base oil solution for 5W-xx
engine oils
- Blend stock/correction fluid for other base
oils
How the market space for Group III and II+
developed in each of these areas and how GTL market development
might follow it is discussed below:
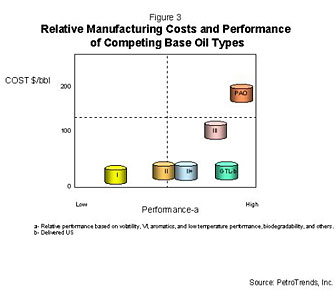
Dirct competition with PAO. Group III base oils
are typically produced by incorporating isomerization of wax fractions
from the base oil into the overall process. The isomerization process
changes the geometry of wax molecules to structures with acceptable
low temperature performance characteristics (they dont form
wax and solidify at cold temperatures). In addition, the isomerization
of wax can significantly boost the VI of the base oil. In fact,
if run under more severe conditions the VI of a paraffinic base
oil can be pushed up to a level that parallels that of PAO. Pushing
VI up does, however, come at the expense of yield. The high VI,
together with very low aromatic content of Group III, put it in
an excellent position to compete with PAO, and that is exactly what
it did when it entered the market.
PAO had enjoyed a nearly unrivaled position
as the synthetic base oil of choice in automotive and
industrial lubricant applications. It captured an estimated 2% of
the total lubricants market. Although PAO offered excellent oxidation
stability and unparalleled low temperature performance it had a
weakness that Group III exploited. Its weakness was manufacturing
cost. The cost to produce PAO was fairly well studied and many were
aware that the minimum costs to produce PAO were significantly higher
than that to produce Group III. It was also well known that although
Group III could beat PAO on a cost basis, PAO still had the virtually
exclusive right to bear the valued synthetic label,
and PAO could far outperform Group III in a cold crank simulator
(CCS). This advantage, however, virtually vanished overnight when
Castrol replaced PAO in its synthetic engine oil formulation with
extra high VI paraffinic base oil. This represented a significant
cost saving in the formulation. It also resulted in a challenge
from Mobil regarding the use of the term synthetic by
Castrol. The challenge was brought to the National Advertising Division
(NAD) of the Council of Better Business Bureaus (CBBB). On April
5, 1999 the NAD announced that Castrol North America could continue
to advertise its product as synthetic motor oil even
though Group III was being used. Group III now had the right to
wear the synthetic lubricants label. Many lubricant
manufacturers switched from PAO to Group III shortly after this
ruling was announced to take advantage of the reduced cost of the
synthetic base oil.
In addition to market opportunities as a replacement
for PAO in automotive applications, Group III has and will continue
to displace PAO in some industrial lubricant applications. Its leverage
in this space is, however, weaker than it is in automotive engine
oils. The automotive engine oil segment ascribes high value to the
term synthetic. The industrial segment places far less
value on the term synthetic and much more value on the
performance advantages they offer. Although the oxidation stability
of Group III is similar to PAO, PAO significantly outperforms Group
III in low temperature applications. As a result, market share capture
by Group III in the industrial lubricants space has come much more
slowly than in the automotive segment.
GTL base oils have an opportunity similar to
the one Group III capitalized on in the PAO market space. The primary
difference, however, is that it will now be competing with both
PAO and Group III. Group III only had PAO to contend with.
The challenge for GTL in this market space,
specifically in synthetic and synthetic-blend automotive applications,
will be cost. Formulators switched from PAO to Group III in automotive
engine oils due to the cost savings one could enjoy by blending
with Group III. Any switch from Group III to GTL would either have
to represent a relatively significant cost savings, and/or measurable
boost in performance. The performance advantages of GTL over Group
III will likely be found on several fronts. On one front, GTL will
promote the superiority of its volatility over that of Group III.
It is believed that GTL will also use additive responsiveness and
total formulation costs as a tool to capture market share from Group
III and PAO. GTL base oils may also provide environmentally
friendly solutions to the industrial lubricants market due
to its biodegradability and its absence of sulfur and aromatics.
Base oil solution for low volatility in passenger
car motor oil. In addition to going head to head with Group III
and PAO in the high performance segment of the automotive lubricants
business, GTL is expected to compete with Groups II+ and III with
a model similar to the one used by Group II, II+ and III to capture
market share from Group I in passenger car motor oil. It did so
by responding to OEM interests in fuel economy and the fact that
the use of lower viscosity engine oils can improve fuel economy.
The use of lower viscosity engine oils (e.g. 5W-30) did not, however,
come without concerns. In addition to the markets reluctance
to embrace lower viscosity engine oil grades, technical hurdles
existed in regard to the ability of the engine oil to stay in grade
during use. Engine oil can thicken and come out of grade when subjected
to the high operating temperatures in an engine due to the light
end boiling off. This meant that although engine oil would yield
desirable fuel economy performance on an engine test stand, it did
not necessarily reflect what was actually delivered in service once
the oil is exposed to heat and aged in operation. In an effort to
address this issue, the International Lubricant Standardization
and Approval Committee (ILSAC) introduced volatility into its GF-2
standard in the mid-1990s.
The first iteration of GF-2 included a comparatively
stringent specification for volatility in multigrade passenger car
motor oil. It was tough, and the volatility of many of the base
oils on the market at that time did not offer the performance necessary
to meet GF-2. Base oil manufacturers had several alternatives. One
option was to narrow the cuts in an effort to compress the hydrocarbon
distribution in the base oils. This solution was considered relatively
costly because, although it would reduce volatility by effectively
cutting off light ends, it also cut off longer chained hydrocarbons
at the other end of the distillation curve. This approach placed
a significant penalty on yields and as a result, was costly. Another
option that could have been used to meet the first iteration of
GF-2 was to blend conventional paraffinic base oil with polyalphaolefin
(PAO). This too, was considered a costly solution because PAO was
over four times the price of conventional base oil. A third option
was to work with ILSAC and other industry stakeholders in an effort
to relax the specifications for volatility in GF-2 and give the
industry more time to prepare. The base oil industry argued that
it was not ready for such a restrictive specification. Agreement
was reached to relax the volatility specification for GF-2 and most
base oil manufacturers were then in a position to meet the requirements.
Most engine oils on the market at that time
did come in under the wire for the final version of GF-2. The process,
however, sent a clear message to the industry that volatility would
be revisited in the next passenger car motor oil specification (GF-3),
and that something other than conventional base oil
would likely be required in the near future for those interested
in competing in the automotive lubricants business.
Although most of the base oil in the US market
was conventional when GF-2 emerged, there was one exception;
Chevron. Chevrons Richmond plant operates with manufacturing
schemes based on hydrocraking and wax isomerization, specifically
Chevrons ISODEWAXINGÔ technology. Rather than removing
impurities with solvents and hydrotreating, this process uses a
hydrocracking process with special catalysts to literally break
the bonds of aromatics and saturate the remains of these and other
constituents in a high temperature, high-pressure atmosphere that
is rich in hydrogen. Unlike conventional solvent refining
where the aromatic content of the base oil is roughly 10%, hydrocracking
typically reduces the aromatic content of paraffnic base oils to
less than 1%. In addition, it typically produces a more refined
cut in terms of hydrocarbon distribution. These attributes, with
the catalytic dewaxing process that increases viscosity index, resulted
in base oils that could meet the more stringent volatility requirements
initially proposed in GF-2 and beyond.
Interestingly, although Group II base oils have
been in the North American market for close to 15 years and demonstrate
superior performance capabilities, they didnt receive much
attention until about the last seven years. The primary reason was
limited supply. As discussed, there were only two producers in North
America when GF-2 emerged Chevron and later Petro-Canada.
This changed, however, when Excel Paralubes (a joint venture between
Pennzoil and Conoco) built a grassroots Group II plant that came
on stream in 1997. The Excel plant increased supply of Group II
by nearly 20 TBD. This additional supply gave Group II the critical
mass necessary to help convince automotive OEMs that the lubricants
industry now had the technology in place required to meet more stringent
specifications around volatility. The new specification represented
a step change in PCMO volatility, as shown below in GF-3.
Table 3
NOACK Volatility
|
|
NOACK Volatility (a)
|
PASSENGER CAR MOTOR OIL
GRADE
|
GF-1
|
GF-2
|
GF-3
|
OW and 5W
multiviscosity grades
|
25
|
22
|
15
|
All other multiviscosity
grades
|
20
|
22
|
15
|
NOTE: (a) D-5800-99 standard test method
for evaporation loss of lubricating oils by the NOACK method.
|
This specification would clearly favor the use
of Group II and pull through demand based on technical need. In
fact, for some grades, the specifications virtually required the
use of Group II and II+. In addition, Group II was also showing
promise as value-added base oil in heavy-duty motor oil applications
and ATF. This too resulted in pull-through demand.
As discussed later in this paper, GTL base oils
likely will be the beneficiaries of the momentum in pull through
demand established by Groups II, II+, and III in automotive engine
oil applications.
BLEND STOCK/CORRECTION FLUID FOR OTHER
BASE OILS
Although base oil manufacturing is clearly shifting
from Group I to Group II in the US and Canada, Group I base oils
are expected to remain an important part of the supply pool. These
base oils are favored as the low cost workhorses for a wide range
of price sensitive industrial lubricant applications. Some lubricant
blenders use Group I because they have captive supply, others use
it because it aligns well with their product portfolios. In many
cases, blenders heavily reliant on Group I base oils will find it
necessary to bring in such high quality base oils as Groups II+,
III, and IV as a means to enhance the performance of the workhorse
Group I. An example of how a blender could use a Group II+ to enhance
the performance of a Group I can be seen in a 10W-30 PCMO formulation.
Although there are many ways to meet the volatility requirements
for GF-3 in a 10W-30, an economical option is to blend with roughly
70% Group I base oil, 10% Group II+, and additives.
GTL base oils are expected to compete with Group
II+, III, and IV as a blend stock to enhance the performance of
Group I base oils. Its ability to displace these competing stocks
is expected to be based primarily on performance and its impact
on total formulation costs.
GTL BASE OIL MARKET SPACE DEVELOPMENT
GTL base oils are positioned to track the footsteps
already established by Group II and II+ as the workhorse in some
multigrade engine oils and as a correction fluid in others. The
challenge for GTL base oils in the US, however, will be the relatively
sluggish market penetration of 5W-30. In addition, Group II and
II+ base oils have already established themselves as the solution
for 5W- and 10W-30 engine oils. This means that additives are well
on their way to being optimized, blenders are comfortable working
with these stocks, and product development costs have been invested.
Rather than potentially giving away value by
competing with Groups I and II base oil in the 10W-30 PCMO market
and others, a more likely scenario is one that allows GTL to maintain
its value by waiting for the direction of specifications to mature
the market into the market space currently occupied by Group III
and IV, and to a lesser extent Group II+. The direction of specification
has already moved a significant volume of base oil demand out of
the Group I space and into the Group II and II+ space in the US
market. Future specifications will continue to push demand through
the Group II and II+ space into the space occupied by Group III,
Group IV and GTL, as shown in Figure 4.
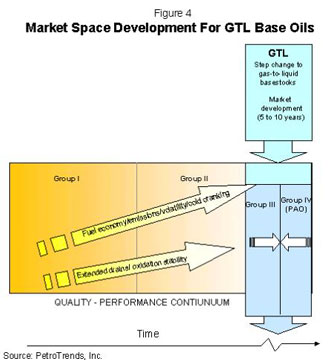
The challenge for GTL in this approach,
however, is that the market will take time to evolve into its space.
This evolution will be tied in a large way to market acceptance
of 5W- and 0W-xx engine oils. The most significant pull-through
demand for GTL base oils in PCMO will, however, likely be tied to
0W-xx. Meeting the volatility requirements in this grades is expected
to be attainable only with PAO and likely GTL. Although the low
temperature performance of GTL base oils could be an issue, data
exist to suggest that this issue can be overcome by GTLs favorable
responsiveness to additives. It is also important to consider, however,
that even with OEMs promoting the use of 0W-xx, consumers have the
final say. If market acceptance of 5W-30 is any indication, consumers
are slow to accept lower viscosity grades even when OEMs recommend
them.
What this means is that GTL will not likely
be a significant demand event in the US for at least the next eight
to ten years. From a product life-cycle perspective, we will likely
see GTL entering the supply pool in the 2005/2006 timeframe. If
one uses the GTL plant completion schedules currently tabled, the
supply build model of Group II/II+ and III, and the grade switching
rates of 5W-30 as a guide to model with, the introduction phase
of the GTL life cycle will likely begin in 2005 and take about five
years before it advances into the growth phase, as shown in Figure
5. Initially it will do so at the expense of Group III and IV base
oils by capturing market share in the synthetic and synthetic-blend
automotive lubricant market space. It will also penetrate the ATF
and automotive driveline market space at the same time. Market acceptance
of GTL is, however, expected to be modest during this introductory
phase of its life cycle due to a limited number of suppliers.
GTL is expected to transition into a growth
phase by capturing demand away from Group II, II+, III, and IV as
demand for 5W- and 0W-xx PCMO increases. As additional supply comes
on line it will give OEMs and blenders the assurances they need
that supply lines are adequate and secure. This will catalyze growth-phase
demand by moving it into a push-demand scenario similar to that
currently occurring with Group II base oils. Push marketing will
drive up demand for GTL in heavy-duty engine oil and industrial
high performance industrial applications.
GTL is also expected to capture significant
market share of the automotive driveline segments over this same
period due to fill-for-life initiatives.
It is also important to consider that although
GTL may not be a significant event in the US over the next eight
years, it will enjoy more aggressive growth in Europe and Asia.
The lubricants market in Europe is more mature than that in the
US and market acceptance of 5W- and 0W-xx is further along.

CONCLUSION
Although the primary focus
of gas-to-liquid (GTL) technology is currently on opportunities
in diesel fuels, base oils derived from this technology could also
be in place by 2005. Base oils produced by GTL processing are expected
to deliver quality superior to Group III and at very competitive
costs.
Base oils produced by GTL
processing are expected to initially enter the lubricants market
by competing with Group III and IV in the synthetic and synthetic-blend
engine oil market space. They will compete with these base oils
primarily on performance and secondarily on price and total formulation
costs. To a lesser extent, GTL base oils will also compete with
Group II+ in a growing market for 5W-30. Rather than reducing the
value of GTL by moving down the quality continuum to Group I and
II base oils, GTL base oils are expected to park themselves in the
high-end market space of Group II+, III, and IV and be the beneficiaries
of specification pushed demand into its space. This will occur by
increasingly stringent performance requirements and market acceptance
of 5W- and most importantly 0W-xx PCMO.
In addition to GTL competing
in the emerging low viscosity passenger car motor oils markets,
it will also penetrate automotive driveline applications, premium
diesel engine oils, high-end industrial lubricant applications,
and white oil applications over the next five to eight years. Adoption
of GTL base oils is expected to occur at a faster rate in Europe
than in the US due to the rate of market acceptance of 0W-xx engine
oils. In addition, GTL will penetrate the Asian market.
Copyright © Petroleum Trends International,
Inc. 2002
|