68th Annual Meeting
National
Lubricating Grease Institute (NLGI)
West Palm Beach, Fl
October
28-31, 2001
THE OUTLOOK FOR GROUP ll/ll+
AND GROUP lll BASE OILS
IN THE U.S. GREASE MARKET
by: Thomas
F. Glenn, President
Petroleum Trends International, Inc.
October 2001
THE OUTLOOK FOR GROUP ll/ll+ AND GROUP
lll BASE OILS IN THE U.S. GREASE MARKET
ABSTRACT
A step change is taking place in how base oils are
manufactured in the US. The industry is moving from the American
Petroleum Institute (API)
Group I products to Group II. In addition the market will see more
Group II+ and III. The aromatic content of the new base oil is significantly
lower than that of Group I. Aromatics are an important factor in
determining soap yields and additive solubility in grease. The lower
aromatic content of Group II base oils can have a negative impact
on soap yields and additives.
Grease manufactures may not be asking for Group II,
but they very well could be using it now and in the future due to
big picture supply and demand issues. Although replacing Group I
with Group II in grease can be a negative experience, PetroTrends
believes Group II/II+ and III will play an increasingly important
role in grease manufacturing moving forward. It may, however, require
grease manufacturers to revisit grease recipes and rethink the economics
of soap making.
INTRODUCTION
At first blush, one might wonder why PetroTrends
is presenting a paper about the outlook for API Group II/II+ and
III paraffinic base oils to grease manufacturers. Many think of
these relatively new types of base oils as products designed primarily
to meet the more stringent volatility requirements in passenger
car motor oils and to better handle soot in heavy duty diesel engines
fitted with exhaust gas recirculation (EGR) pollution control devices.
In addition to engine oils, Group II/II+ and III also add
value to automatic transmission fluids. Although Group II/II+ and
III can also add value to a wide range of industrial lubricants,
this segment of the market was not the driver for higher quality
base oils.
So why give a paper on the outlook for Group
II/II+ and III base oils in the grease market? In short, because
you may be using Group II/II+ base oils now or in the future as
a result of changes that have, and will continue to take place in
the base oil business. In addition, Group III base oil could offer
opportunities as a new and lower cost “synthetic” base oil.
BASE OIL USE IN GREASE
Base oil is a major component in grease. It
typically represents 80% to 90% of the finished product volume.
Grease manufacturing commonly starts by forming soap in base oil.
This process, known as saponification, is typically carried out
by introducing base oil to a kettle along with fatty acids (usually
in the range of C12 to C22 ) and alkali.
An acid-base reaction occurs when these components
are heated and mixed and a “soap” thickener is formed. This saponification
process, commonly referred to as “cooking” takes roughly two hours
to complete and is often carried out in a kettle containing 20%
to 30% of the base oil volume that will be used in the final product.
Fillers and such additives as antioxidants, extreme pressure (EP),
rust inhibitors, and others are added after the soap is formed.
The balance of the base oil (typically paraffinic) is also
added to the batch at this time. Naphthenic base oils are preferred
in the “cooking” process because the fatty acids and alkali used
to make the soap are solubilized in the aromatics that are present
in naphthenic base oils.
Naphthenic base oils historically had an aromatic
content of roughly 23%, whereas they were roughly 10 12% in paraffinic
base oils. A good soap yield for a NLGI No. 2 grease with a naphthenic
base oil is upwards of 17% or higher, while paraffinic base oil
will yield about 11% to 12% in the same grease.
The higher aromatic content of naphthenics imparts
greater solubility, therefore higher soap yields. Since fatty acids
and alkali are leading contributors to the cost of the grease, soap
yield is a critical issue in grease making. Although naphthenics
are preferred due to better yields, the use of paraffinic base oils
in the saponification and finishing process has grown in recent
years. This trend is driven by tighter supply of naphthenics and
the base oil industry’s move to reduce the aromatic content of naphthenics
in response to environmental issues. Base oil inventory is also
an issue that guides base oil selection.
Although naphthenic base oils may produce better
yields, the challenge of procuring naphthenics when supply is tight
and the tankage required to store it for use primarily in grease
can also push paraffinic base oils in favor of naphthenics. This
is especially true when a manufacturer has a product slate relatively
light on grease and heavy on other lubricants where the use of naphthenics
may be undesirable.
In addition to issues of price, availability,
and inventory, the types and grades of base oils used in each step
of the grease manufacturing process is a function of the type of
grease made. The same issues that guide base oil selection in regular
lubricants guide the base oil viscosity selection for grease. The
typical viscosity grade used in the industry is 500 SUS at 100°C.
The use of 800 SUS is also very common in most automotive grease
applications. Bright stock (1,500 SUS) is typically used to make
grease for heavy-duty applications, typical of steel mills. Additives
are also frequently used with antioxidants being the most common,
while such others as EP additives are occasionally used in steel
mills and other heavy load applications. Rust inhibitors are also
frequently used.
PARAFFINIC BASE OILS A CHANGING BUSINESS
As far back as most in the lubricants business today
can remember, paraffinic base oils have been made by a process scheme
utilizing solvent-refining, hydrotreating, and solvent-dewaxing.
The first step in this manufacturing scheme is to fractionate the
feed used for base oils. This is typically done by producing three
cuts, or viscosity grades (light, medium, and heavy). Each grade
is then typically run through a solvent refining and hydrotreating
process to reduce the level of such contaminants as sulfur and aromatics.
This step improves the color of the base oil, its oxidation stability,
and other performance characteristics. This is followed by solvent
dewaxing process to remove long chain linear paraffins. Long-chain
linear paraffins are undesirable because they can result in formation
of wax crystals at cold temperatures and significantly compromise
the cold flow characteristics of a lubricant.
Paraffinic base oils produced by this process, often
referred to as “conventional base oils,” were the workhorses of
the industry. They accounted for nearly 85% of the total base oil
consumed in the US for most of the last decade. Naphthenics accounted
for much of the balance. A relatively small slice of the pie in
terms of volume was enjoyed by polyalphaolefins (PAO), polyolesters,
phosphate esters, and other synthetic basestocks.
Although paraffinic base oils were often “tweaked”
to improve performance, much of the burden to enhance the performance
of finished lubricants prior to the early nineties was placed on
additives, and or a bump up to “synthetic” base oils. This, however,
changed with the introduction of the International Lubricant Standardization
and Approval Committee (ILSAC) performance category GF-2 engine
oil specification in passenger car motor oils. To understand where
we are today with base oils and how it could impact grease requires
a base of knowledge about ILSAC and passenger motor oil (PCMO).
Introduced in the mid 1990s, the first iteration of
GF-2 included a comparatively stringent specification for volatility
in multigrade passenger car motor oil. Volatility emerged
as an issue in passenger car engine oils due to fuel economy and
emission standards. In order to meet more challenging fuel economy
initiatives, automobile manufacturers were faced with the need to
move to lower viscosity multigrade engine oils (e.g. 5W-30 versus
10W-30). Lower viscosity multigrades allowed for increased fuel
economy by reducing the parasitic load associated with the lubricant
itself. It was found, however, that 5W-30s and other lower
viscosity engine oils would thicken in use due to the evaporative
loss of the light ends in the base oil. As a result, fuel
economy at the start of an engine test would not necessarily reflect
what one could expect with the same engine oil used in actual service.
In addition to the issue of fuel economy, the evaporative loss of
light ends was also considered an issue because of the potential
that it could carry lubricant additives (phosphorus in particular)
to the exhaust system and poison the catalytic converter.
In an effort to address this issue, ILSAC established
a volatility hurdle for all multigrade passenger car motor oils.
The first hurdle was seen in GF-2 and the first iteration of it
sent a chill through the base oil manufacturing industry. It was
tough, and the volatility of many of the base oils on the market
at that time did not offer the performance necessary to meet GF-2.
Base oil manufacturers had several alternatives. One option was
to narrow the cuts on their distillation towers in an effort to
compress the hydrocarbon distribution in the base oils. This solution
was considered relatively costly because, although it would reduce
volatility by effectively cutting off light ends, it also cut off
longer chained hydrocarbons at the other end of the distillation
curve. This approach placed a significant penalty on yields and
as a result, was costly. Another approach that could have been used
to meet the first iteration of GF-2 was to blend conventional paraffinic
base oil with polyalphaolefin (POA). This too was considered a costly
solution because PAO was over four times the price of conventional
base oil. A third option was to work with ILSAC and other industry
stakeholders in an effort to relax the specifications for volatility
in GF-2. The argument being that the base oil industry was not ready
for such a restrictive specification at that time, and to enforce
one could limit the availability of OEM-recommended engine oil to
the motoring public. Agreement was reached to relax the volatility
specification for GF-2 and most base oil manufacturers were then
in a position to meet the requirements with a reasonable level of
investment. The final specification for volatility in GF-2 and how
it compares to GF-1 is shown below:
|
NOACK Volatility-a
|
PCMO grade |
GF1 |
GF2 |
0Wand5Wmultiviscosity
grades |
25 |
22 |
All other multivisosity grades |
20 |
22 |
a - D5800-99 Standard Test Method for Evaporation Loss of Lubricating
Oils by the Noack Method
Most engine oils came in under the wire for
the final version of GF-2. The process, however, sent a clear message
to the industry that volatility would be revisited in the next passenger
car motor oil specification (GF-3), and that something other than
“conventional” base oil would likely be required in the near future
for those interested in competing in the automotive lubricants business.
Although most of the base oil in the US market
was “conventional” when GF-2 emerged, there were some exceptions.
Chevron and Petro-Canada represented two exceptions. Both companies
were operating with manufacturing schemes based on hydrocraking
and wax isomerization, specifically Chevron’s ISODEWAXINGÔ. Rather
than removing contaminants with solvents and hydrotreating, this
process uses a hydrocracking process with special catalysts to literally
break the bonds (crack) of aromatics in a high temperature, high-pressure
atmosphere that is rich in hydrogen. Unlike “conventional”
solvent refining where the aromatic content of the base oil is roughly
10%, hydrocracking typically reduces the aromatic content of paraffnic
base oils to less than 1%. In addition, it typically produces
a more refined cut in terms of hydrocarbon distribution. These attributes,
with the catalytic waxing process that increase viscosity index,
resulted in base oils that could meet the more stringent volatility
requirements initially proposed in GF-2 and beyond. In an effort
to differentiate these “unconventional” base oils from “conventional”,
the API created definitions for three groups of paraffnic base oils,
as highlighted in Table 2.
Table 2
American Petroleum Institute Paraffinic Basestock Groups
|
|
Requirements
|
API Group
|
Sulfur, % wt.
|
Saturates, % wt.
|
Viscosity index
|
l
|
>0.03
|
<90
|
80-120
|
ll
|
<0.03
|
>90
|
80-120
|
lll
|
<0.03
|
>90
|
>120
|
lV - a
|
-
|
-
|
-
|
V - b
|
-
|
-
|
-
|
a - includes polyalphaolefin (PAO).
b - includes esters and other basestocks
not included in API Groups l through lV.
|
Group II and III base oils are generally considered
superior to Group I because they have a lower aromatic content.
Aromatic fractions tend to be more unstable than saturated hydrocarbons,
and as a result, Group II basestocks have superior thermal stability
and resistance to oxidation over Group I. In addition, as you move
up the continuum from Group II to III, you move from base oils with
a minimum viscosity index (VI) of 95 to Group III base oils with
minimum VI over 120. This higher VI, together with other issues,
makes Group III base oils an ideal blend stock to meet the more
stringent volatility requirements in passenger car motor oil l.
In addition, it gives these base oils an advantage in heavy-duty
motor oil, and ATF.
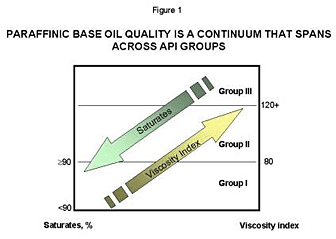
Although the API Group classifications do provide
clear guidelines to differentiate conventional and unconventional
base oils, it is important to consider the differences between API
Groups as a quality continuum based primarily on saturates and VI,
as shown in Figure 1.
The value of this perspective is illustrated
in the “Group II+” designation for base oil. Although Group II+
is not an official API definition, it emerged out of the need to
describe a base oil with a meaningfully higher viscosity index than
the 100 that is typical of most Group II base oils. Group II+ base
oils will typically have VI in the range of 108 to 115. These base
oils offer performance advantages over typical Group IIs in some
passenger car motor oil applications. Viewing the base oil grades
as a quality continuum also assists in appreciating the value that
not all Group II base oils are equal. This can be a very important
issue for grease manufacturers using Group II base oils since both
the aromatic content and VI of a Group II can be different and consequently
result in different soap yields and additive solubility, as discussed
later in this paper.
Interestingly, although Group II base oils have
been in the North American market for close to 15 years and demonstrate
superior performance capabilities, they didn’t receive much attention
until about the last seven years. The primary reason was
limited supply. As discussed, there were only two producers in North
America when GF-2 emerged Chevron and Petro-Canada. This
changed, however, when Excel Paralubes built a Group II plant that
came on stream in 1997. The Excel plant, a joint venture between
Pennzoil and Conoco, increased supply of Group II by nearly 20 TBD.
This additional supply gave Group II the critical mass necessary
to help convince automotive OEMs that it was now time to write more
stringent specifications around volatility that represent a step
change in PCMO performance. This specification would clearly favor
the use of Group II. In fact, for some grades, the specifications
virtually required the use of Group II and II+. In addition,
Group II was also showing promise as value added base oils in heavy-duty
motor oil applications and ATF.
The Group II base oil capacity brought on stream
by the Excel plant sent a clear signal to all finished lubricant
producers that Pennzoil - one of the leading marketers of PCMO -
was committed to Group II base oils and this could give them a competitive
advantage over those with only Group I. In addition, Chevron and
Petro-Canada would now have additional support in promoting the
advantages of “unconventional” base oils and would likely
gain more traction in the marketplace. The Excel plant had another
equally significant impact on the market. This facility added close
to 10% additional capacity to the US base oil supply pool. Together
with an expansion project by Petro-Canada and the capacity creep
of others, the US had a paraffinic base oil supply overhang approaching
nearly 15% in 1997. Base oil prices quickly dropped as the market
sought to correct for the over capacity. Several smaller base oil
plants were closed because they did not have the economies of scale
to compete, or the business to justify investments in Group II.
These exits, together with decisions by others to install new technology
and close Group I base oil plants, reduced the ranks of paraffinic
base oil plants from 22 in 1991 to 15 in 2001. In addition, the
closures reduced the number of Group I suppliers by six plants.
Interestingly, however, this did not have a significant impact on
total base oil capacity volume. In fact, with the nearly 10% total
increase in capacity added to US base oil pool by from the Excel
facility, and capacity creep at surviving plants, the US capacity
for paraffinic base oil reached nearly 169.7 thousand barrels a
day (TBD) in 2001, up from 161.4 TBD in 1991. Group I base oil currently
accounts for 90.7 TBD, or 53% of the total produced in the US, as
shown in Table 1.
Although paraffinic base oil capacity was not
reduced over the last ten years, there was a signficant drop in
naphthenic base oil capacity. Total naphthenic base oil capacity
reached only 50.1 TBD in 2001, down from 59.5 TBD in 1991. A large
percentage of this decline is attributed to Exxon converting a naphthenic
base oil processing plant over to one that produces paraffinic base
oils. This decline in capacity has driven some to replace naphthenic
base oils with paraffinic in grease.
In addition to Group II, Group III base oils also
enjoyed a significant boost in visibility and popularity over the
last few years. The primary driver for this was an announcement
by the National Advertising Division (NAD) of the Council of Better
Business Bureaus (CBBB) on April 5, 1999 that Castrol North America
could continue to advertise one of its products as synthetic
motor oil. This announcement was made in response to a challenge
by Mobil that the Castrol product was not synthetic
because it used Group III rather than PAO base oils. The NAD announcement
meant that Group III base oils now had the right to wear the elite
synthetic lubricant label. This was a particularly important
milestone for Group III since its cost, and therefore, market
price was significantly lower than PAO. Many majors quickly replaced
PAO with Group III in their synthetic engine oils in an effort to
enjoy these cost advantages,
The market changes described above set the stage for
todays base oil business and how they can impact the grease
business. In summary, these changes include:
- A step change in manufacturing technology from solvent
refining and solvent dewaxing to hydrocraking and isodewaxing
- Emergence of API Group I, II, II+, and III
(a quality continuum based primarily on saturates and VI)
- A paraffinic base oil supply pool with significantly
less aromatic content; similar situation with napthehnics
- No significant change in overall capacity
to produce paraffinic base oils
- But, significantly fewer suppliers
- Significant reduction in supply of conventional
Group I base oils
- Acceptance of Group III as a synthetic
base oil
WHAT DO THE CHANGES MEAN FOR GREASE MANUFACTURES?
Although Group II/II+ and III base oils emerged
primarily to meet the needs of automotive lubricants; they are,
and will continue, to impact grease manufacturers. In just under
ten years, the volume of Group II base oil in the US supply pool
increased from 10% of the total to 47% and the shift from Group
I to Group II manufacturing is expected to continue. For grease
manufacturers this means that Group II may have replaced Group I
in their operation with little to no fan fare. It may have simply
replaced Group I when a base oil supplier switched production from
Group I to II. This would have likely have been received as a higher
quality base oil for nearly the same price as Group I when
the switch first occurred. In fact, for most applications this would
be true; it was nearly a quality giveaway when initially introduced,
because Group II did not enjoy a premium over Group I. Today, however,
Group II base oil enjoys a price premium of nearly $0.10 a gal over
that of a Group I.
Group II base oil could also replace Group I
in the grease kettle, with little to no fanfare, because it may
be brought in to meet the more stringent specifications of the higher
volume automotive lubricants. Some lubricant manufactures must use
Group II/II+ due to specifications. As such, it was considered to
be only an issue in this automotive lubricant segment and again
a quality giveaway in other applications, including grease.
What could easily be overlooked in the big picture
of the switching dynamics from Group I to Group II, is that soap
yields in grease are heavily dependent on the aromatic content of
the base oil used during saponification. A switch to Group II typically
drops the aromatic content of base oils to less than 1%, down from
nearly 10% in a Group I. This drop could leave grease manufacturers
scratching their heads, because although they had not made any perceived
changes in the product or production processes, grease yields are
down and additive solubility is now an issue.
Although Group II/II+ and III base oils can
have a negative impact on soap yields and be a challenge to work
with in terms of additive solubility, the grease industry is just
starting to come up the learning curve with its use. The use of
Group II/II+, and potentially Group III, could prove to offer both
performance and marketing advantages in grease. As discussed, Group
III has now been accepted into the fold as a synthetic
base oil and it costs significantly less than PAO. This offers grease
manufacturers the potential to make synthetic greases
at significantly lower cost than if PAO were used. It is important
to consider, however, that the value proposition for synthetic
in industrial lubricant applications is quite different than it
is in consumer automotive products.
Group II and II+ could prove to be advantageous
in grease manufacturing due to its superior oxidation stability.
The oxidation stability of these stocks nearly parallels that of
PAO, which is an important factor in some grease applications. In
addition, the time and materials required to add antioxidant to
grease may not be required when using Group II base oil
Finding a positive outlook for Group II/II+
and III base oils in the saponification process is expected to be
a much greater challenge. Group II base oils are valued in a large
part for their high saturates level. Base oils used in the saponification
process are valued in part for their aromatic content. Group II
moves away from the value proposition in soap making, not towards
it. This reality is expected to give rise to a greater use of preformed
soaps. By purchasing preformed soap and working to optimize additive
performance in Group II/II+ and IIIs, grease manufacturers may be
in the position to make better grease at a lower cost. Doing so
will, however, require time to work with the new base oils and conduct
a careful comparison of the total costs required to make a soap
(inclusive of labor costs, energy, raw materials, and others) versus
that of buying a preformed soap and adding base oil.
In conclusion, PetroTrends believes Group II/II+
and III will play an increasingly important role in grease manufacturing
moving forward. It may, however, require grease manufacturers to
revisit grease recipes and rethink the economics of soap making.
Copyright © Petroleum Trends International,
Inc. 2002
|